Within the bustling world of logistics and supply chain management, warehouse, distribution and fulfillment hubs have staffed up to meet the frenetic demands of a Retail sector that continues to perform robustly. At peak times, hiring surges and increased inventory levels can lead to less efficient production and more unsafe incidents, especially for businesses generating high volumes of paper and secondary packaging recyclables in the form of old corrugated cardboard (OCC).
Caution: Pallet clutter from used paper, cardboard and other packing materials make warehouse and distribution centers difficult – and dangerous – places to navigate. New and temporary workers often lack adequate safety training in the handling of heavy, one-ton recycling bales (see sidebar), increasing the risk of injuries and causing a negative impact on productivity. In addition to protecting employees, utilizing space properly and implementing safe practices can make for a more productive workplace. Numerous studies have shown the link between health/safety and employee productivity.
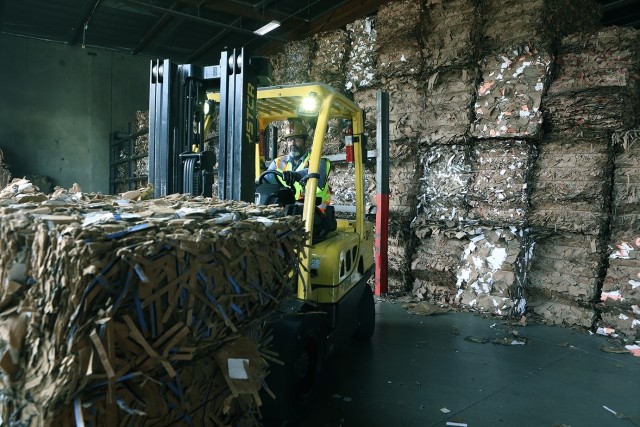
Smart manufacturing and distribution operations understand that optimizing warehouse safety pays dividends. A safer center for work means more productive employees and a lower chance of accidents. From infrastructure to processes and people, a holistic approach to safety ensures not only compliance but also a more productive and harmonious work environment with lower costs. Safety is an investment that always pays off in terms of employee well-being.
It’s no secret that productive employees are an asset to any organization, and there is a direct correlation between productivity and safety. It should seem obvious that production depends on keeping employees safe. The safer the work environment, the more productive it is. While that idea may seem like a “no-brainer,” the rationale is lost on many workplace supervisors who equate safety with meeting governmental, regulatory compliance. For them, employee safety often is perceived to be an impediment to operations.
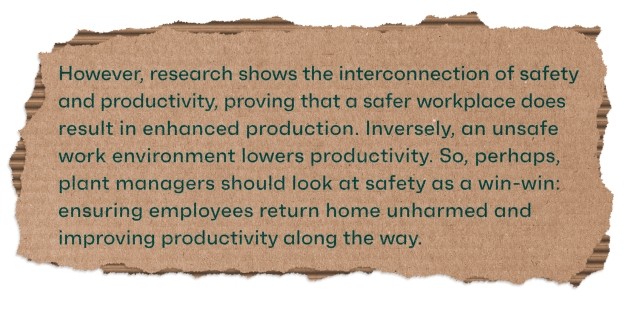
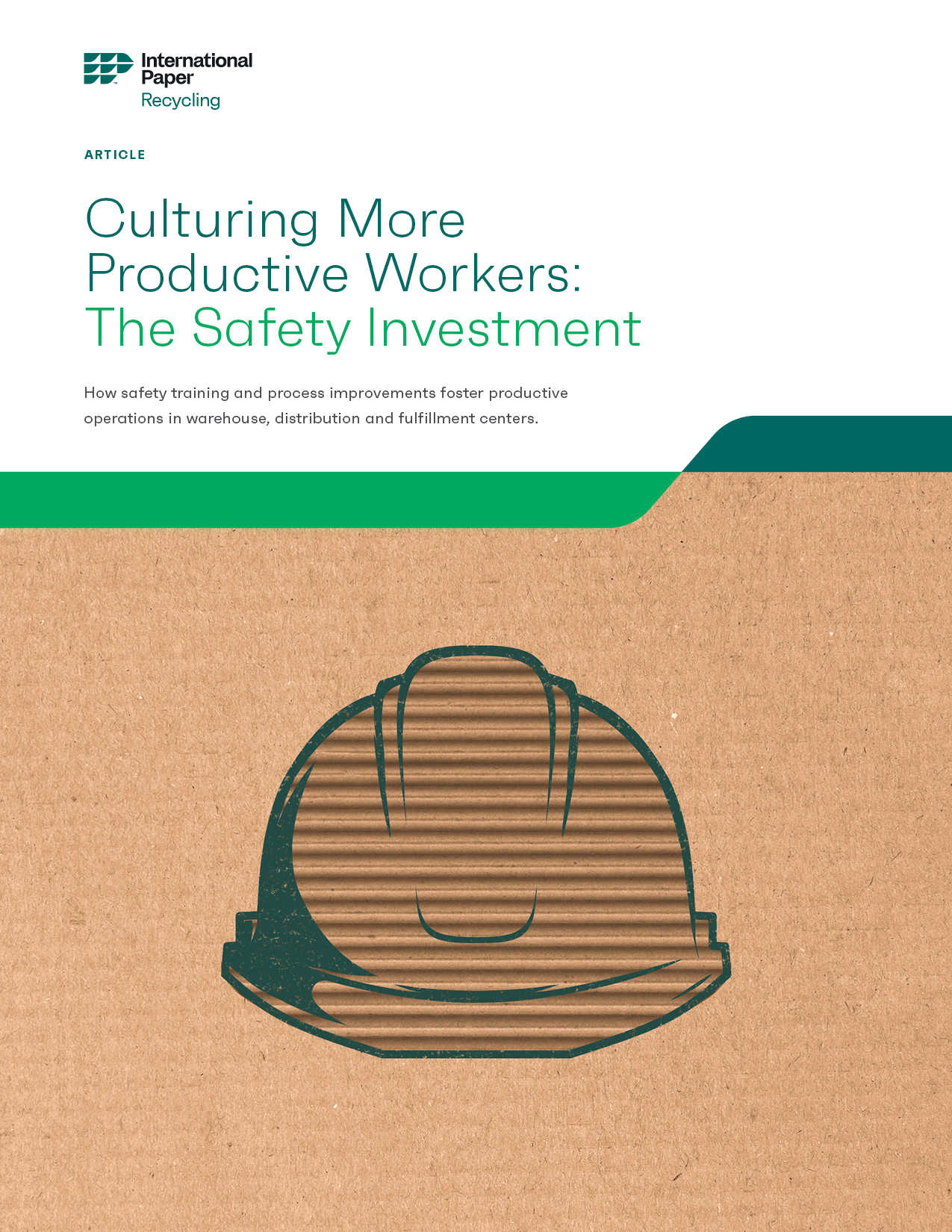
Safer = Better Productivity?
Key considerations for the people managing these ramped-up workforces during peak months for warehousing and fulfillment centers handling recyclable packaging materials:
- A safer warehouse means fewer disruptions, less downtime and a more focused workforce.
- Research has shown that employees who feel their workplace is safe are more likely to perform better than those who feel unsafe.
“When safety improves, so does productivity,” wrote Gen Handley in EHS Today (Environmental Health and Safety). According to a study in Occupational Health Science, “employees’ safety and health are of primary importance, as both are key elements in achieving an organization’s desired productivity and efficiency.” Furthermore, according to Occupational Health & Safety magazine, “the benefits of focusing on accident prevention are two-fold: a reduction in accidents and a boost in operational efficiency, making it a win-win situation for everyone involved.”
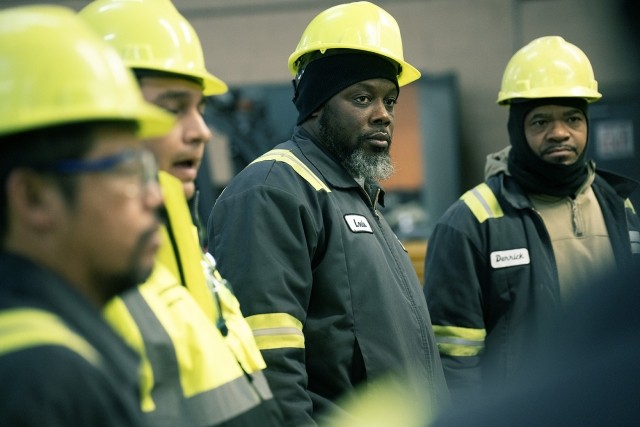
Leaders of progressive companies treat safety as an investment in productivity, and they look for a return on their investment (ROI). The average return on workplace safety programs is approximately $5 for every $1 invested, according to the Occupational Safety and Health Administration (OSHA).
Businesses that invest in safety have happier, more productive employees, which is a strategic advantage when it comes to two key bottom-line factors*:
- Lower injury-related costs
- Better long-term business viability
In today’s fast-paced world of supply chain fulfillment and chronic labor shortages, it is more important than ever to ensure worker safety, especially in warehouse/fulfillment environments. Each year, nearly six of every 100 warehouse employees suffer a workplace injury, reports the U.S. Bureau of Labor Statistics. As a result, 4.6% have had to take time off work or be transferred to a different facility. These injuries have a major impact on business P&L (profit and loss) statements.
Employers pay nearly $1 billion weekly for direct workers' compensation costs alone, adding up to more than $50 billion per year! Medical bills, insurance premiums, equipment repairs and hefty OSHA penalties add to that expense. While the financial burden is significant, the indirect costs to employee mental and physical health, as well as to their families and loved ones, are even greater.
The end goal of plant management should be to make safety best practices second nature for all full- and part-time employees. “Prioritizing warehouse safety isn't just a legal obligation; it's a moral imperative and a sound business practice,” concluded Ryan Garratt in a LinkedIn post. “By implementing proper training protocols, robust safety procedures and fostering a culture of safety awareness, you can safeguard your employees' well-being while simultaneously boosting productivity and efficiency in your warehouse operations,” believes Garratt, who presides over a trio of Canadian companies (Staff Depot, 1st Choice Staffing and Drivers Depot) that specialize in temporary, temporary to hire and permanent warehouse staffing.
(* Source: logistics provider Kenco Group)
Safety Above All Else
At IP, safety is our most important responsibility, and we believe anyone who steps foot in an IP facility has the right to put a stop to any unsafe situation. Hear from our team members around the world as they express "I have the right."
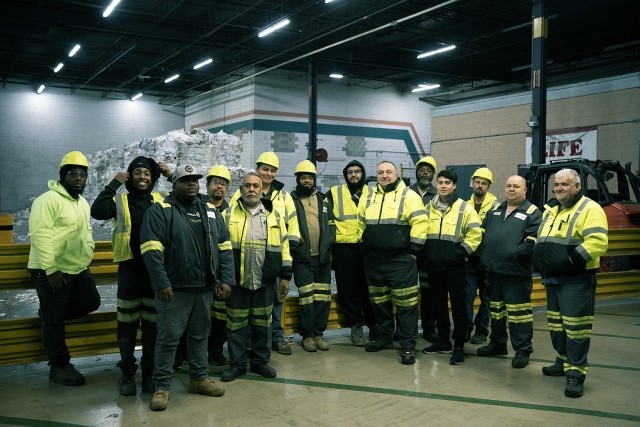
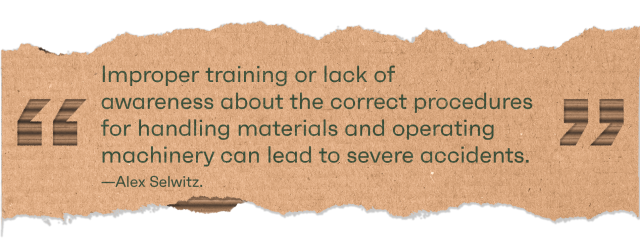
Lift-truck Safety
The risk of injury is ever-present in industrial work spaces. Loading docks are a hive of activity but also potential danger zones. OH&S magazine counts material handling and machinery operation among its top five culprits. “Improper training or lack of awareness about the correct procedures for handling materials and operating machinery can lead to severe accidents,” writes Alex Selwitz. “This includes... the operation of heavy machinery like forklifts.”
Indeed, the most common types of workplace accidents include material-handling accidents, agrees Inbound Logistics magazine. Unsafe use of forklifts is the most often cited hazard in warehousing operations by OSHA.
Every year, 100 people are killed and 95,000 people are injured in forklift accidents, reports the office of California workers’ compensation attorney Matthew Russell. The most common accidents involve overturned forklifts, which can crush and seriously injure or kill the employee.
Training is the cornerstone of warehouse safety. Implementing guidelines, such as designating specific areas for loading/unloading and using equipment like dock levelers, can enhance safety. Workers should also be trained to handle goods without causing damage or injury, particularly with forklifts. Regular sessions can educate workers on potential hazards, how to avoid them, and what to do if they encounter one. Specialized training, including how to operate a particular machine, should also be mandated.
From truck driver safety and on-site occupational health nurses to the proper and safe baling of old corrugated cardboard (OCC), IP is committed to the health and safety of all employees including those involved in the process of recycling compressed cardboard bales. We know that ensuring the safety of full-time employees, seasonal workers and contractors is important to our partner companies as well.
Earlier this year, International Paper (IP) developed an animated tutorial highlighting loading requirements for baled material.
“We created a step-by-step video guide demonstrating the safe loading and proper stacking of bales at the door of the trailer,” Levell Hairston, VP/GM of IP Recycling” told CSRwire, a news source focused on corporate social responsibility operated by 3BL Media network. “The process is a requirement for IP suppliers, and we hope the industry can take advantage of this training tool as well.” The tutorial covers the acceptable bale-loading patterns, stressing the importance of:
- Inspecting the Trailer
- Checking Bale Integrity and Wiring
- Identifying Unsafe Door Loads
Taking all the above into consideration, we have seen the very real impacts of safety on productivity and performance, as well as liability containment. With all factors considered, it is readily apparent that building a culture of safety is not just the right thing to do, safety is good business.
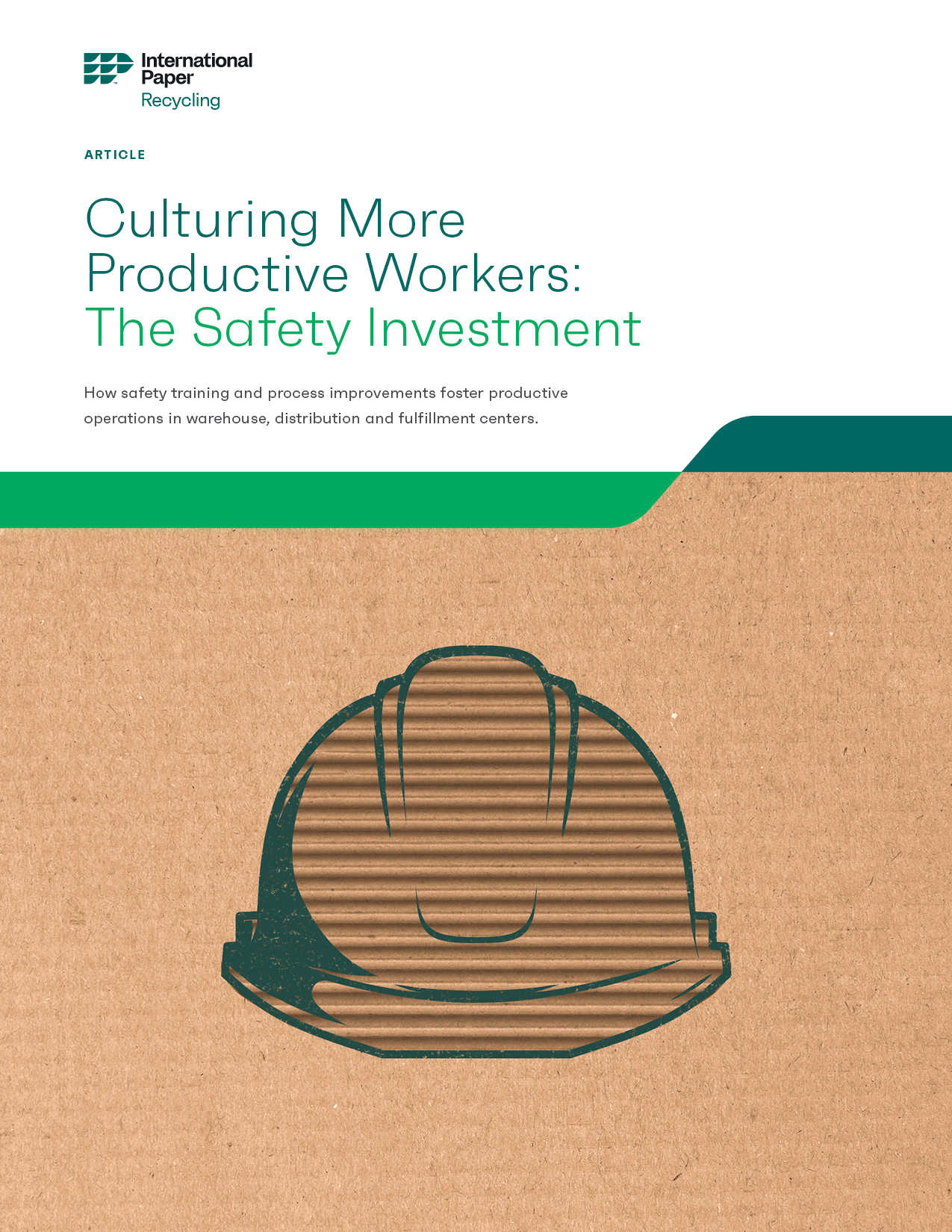