Too Big or Too Small: Extreme Range of Volumes Bedevils Operations Management
With more than 2,500 supermarkets serviced by 40-plus distribution centers, this client serves 60 million households across 35 states, and the numbers continue to grow through an aggressive acquisition strategy. Stores range in size from as small as 57,000-square-foot grocery stores stocking 10,000 items, to 250,000-square-foot giants with an even wider selection of product categories including apparel, sporting goods, and even home furnishings.
Unpackaging goods for shelf placement and replenishing inventory generates a lot of empty cardboard boxes, or old corrugated containers (OCC), as they are known in the recycling industry. To manage the ongoing removal of massive volumes of OCC more efficiently, our client placed balers at every retail location. Most stores truck their bales of OCC to the client’s nearby distribution centers, where loads are consolidated. But some individual stores need the bales picked up right in back of the store.
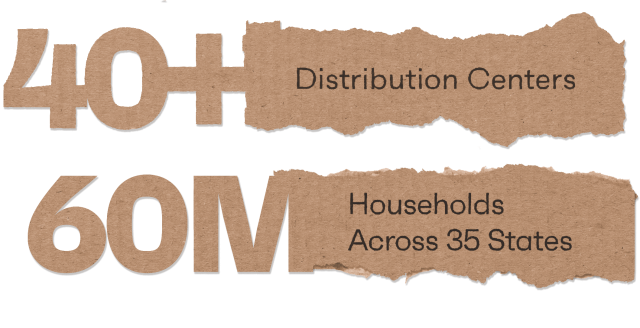
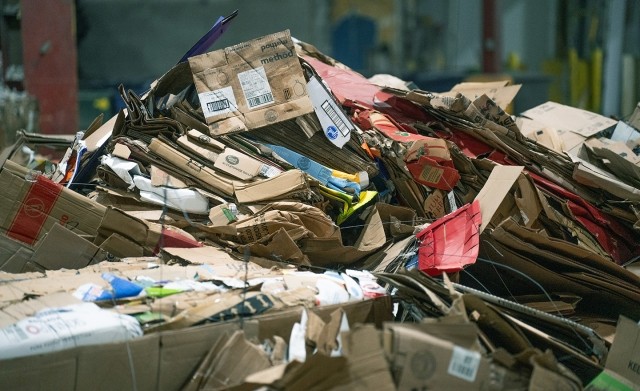
.
Existing suppliers were not meeting the client’s needs, according to Joshua Starrett, IP’s Commercial Manager, Recycling.
“They were having service challenges at distribution center sites. OCC was not being collected on a timely basis,” Starrett said. There was also the risk of food safety issues, as OCC backed up, potentially putting the client out of compliance with FDA rules. “And there were operational challenges that forced some stores to dump bales of OCC at landfill sites.”
This national grocery retailer needed a reliable recycling partner with the flexibility and scale to handle its range of volumes, while accommodating the differing schedule requirements across locations—multiple daily pickups at its big distribution centers, down to two or three times weekly at individual stores. Publicly traded, the client required data to document the effectiveness of its recycling efforts for its ESG reports. The grocer turned to IP for a solution.
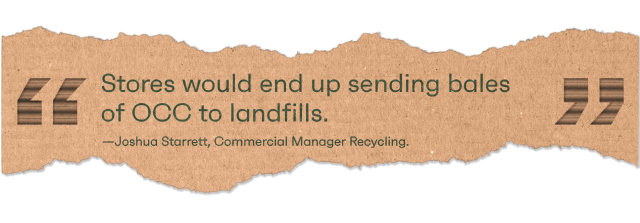
Integrated, Tailored, Scalable Solution
The client first tapped IP in 2016 for a strategic relationship. Able to offer the scale, speed, and geographic reach required, IP demonstrated its capability to move quickly, installing industrial capacity balers at three of the client’s distribution centers. Because of IP’s deep expertise, it was able to identify opportunities for significant savings by optimizing logistics at specific sites.
“We showed them different ways to manage their OCC recycling program,” says Starrett. At a Midwest frozen food distribution center, for example, IP suggested the client backhaul bales of OCC using its own empty delivery trailers on the return trips from individual stores.
“It is not a small distribution center. We knew we would be able to save them tens of thousands of dollars with that one idea,” said Starrett. “It was the size of this grocery chain that presented an opportunity. We helped them to actually leverage their scale to dramatically improve OCC recycling efficiency.”
At the smaller end of the client’s operations were individual retail outlets—100 of them— that needed back-of-store pickup. These back-of-store volumes range from daily to once every one or two weeks. IP services all these sites, either through IP’s own fleet, or by partnering with third-party haulers that the IP Recycling Team oversees.
In the next phase, IP’s recycling services were added at several more of the client’s distribution centers. Following a recent RFP, even more volume was awarded to IP, which now handles 10 of the client’s distribution centers, at volumes as high as 100 tons a day—five truckloads daily.
During seasonal peak periods, the volume increases, requiring up to seven truckloads daily. On an annual basis, that’s 280,000 tons of OCC collected. IP also offers the client a rebate for the market value of the OCC that is reclaimed and reused in IP’s paper mills, which is an added revenue stream to the grocer.
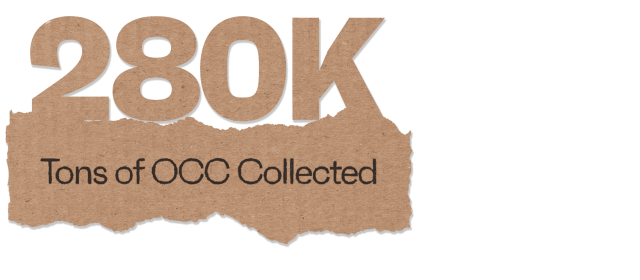
Circularity Data Solutions
Much of this OCC is reused in IP’s own mills for conversion into new fiber-based packaging that the client relies on to service its customers. All materials are tracked, ranging from waste tonnage retrieved to recycling rates of OCC. The client has set ambitious goals for sustainability, seeking to attain 100 percent recyclable, compostable and/or reusable packaging, and to increase the amount of recycled content in its packaging, both by 2030.
“They saw the integrated value of working with IP two years ago in preparing that RFP, and in working with U.S.-based sourcing for recycling services,” said Starrett. “We are able to provide consolidated reporting for all 10 distribution centers, and for all the 100+ stores we service.”
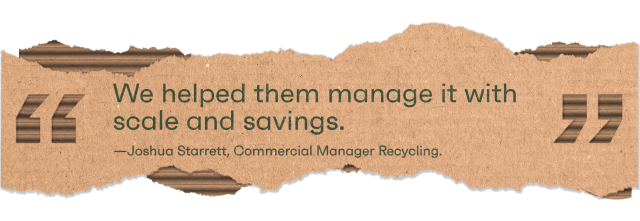
Your Partner for the Future
International Paper’s Sustainability in Motion® offers customized solutions including baling, hauling, and data reporting. These solutions, tailored to each customer location, in many cases include rebates based on the market value of your waste fiber, which IP converts to new packaging products at its many mills. With a potential new revenue stream, IP can bring your circularity efforts to a new level, with recycling services and integrated mills providing full-circle solutions for your business.
International Paper is your recycling partner for the future. We are your best end-to-end, closed-loop sustainability partner. We design custom solutions for businesses of all sizes, with a focus on maximizing your economic and sustainability value at every point. For International Paper, recycling is a culture, not a commodity.
Let International Paper put Sustainability in Motion® for you.
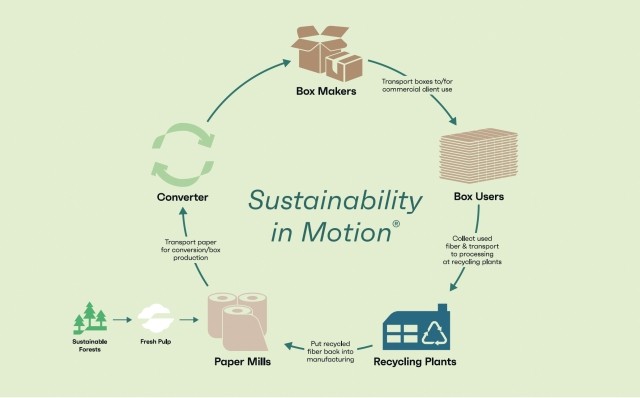
Contact us to get your recycling solution started with a free on-site assessment
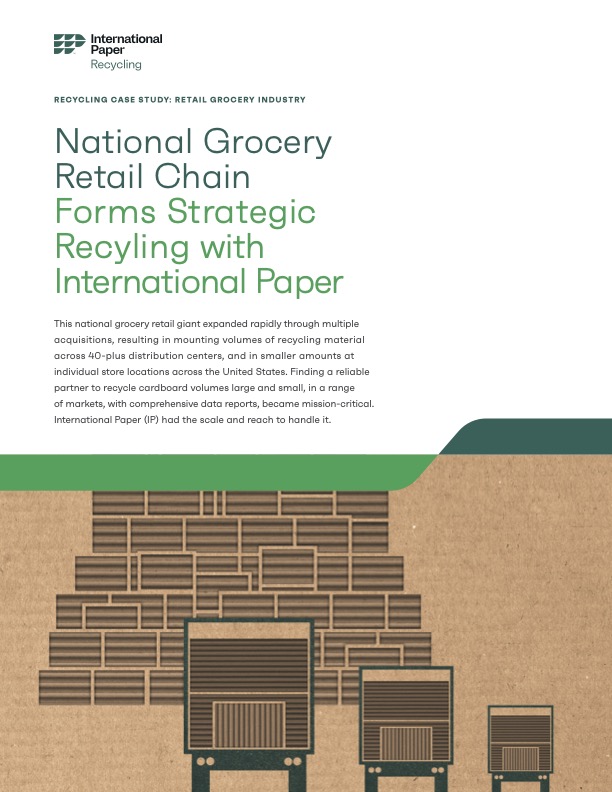